Don’t let corrosion turn your classic into Swiss cheese
Pitting corrosion occurs when a small hole develops in a protective coating on a metal surface exposing it to the atmosphere. A galvanic corrosion reaction can occur with the large damaged coating acting as a cathode and the small amount of exposed metal acting as an anode. Because of the large difference is size between the anode and cathode, a high demand for electrons is placed on the anode causing intense corrosion and rapid damage to the metal structure. What makes matters worse is that very little corrosion is visible on the surface. A small amount of visible rust will form on the surface of the hole whilst the real damage is being done inside the metal where it is literally being dissolved away.
The pitting reaction is enhanced when the metal is in contact with a solution containing chloride, fluoride or bromide ions. Taking salt water as an example, iron atoms will dissolve into the water solution giving up electrons as they do. The electron then flow to the cathode and are discharged. As a result the liquid inside the pit gains a positive charge whereas the liquid outside the pit has a negative one. Negatively charged chorine ions in the water are attracted into the pit which increases the acidity of the liquid inside.
As the acidity grows so does the rate of reaction and the speed at which the metal in the pit dissolves.
Metals that are most susceptible to pitting include: stainless steel, chromium, passive iron, aluminium and copper.
There are two major types of pitting corrosion – Through Pits and Sideways Pits. Through Pits are basically pits that go straight down through the metal from the surface hole. With Sideways Pits, an initial pit is formed below the surface hole and then metal is eaten way horizontally underneath to form large undetected cavities.
Because of the very clandestine nature of corrosion pits detecting them and the extent that they have impaired the integrity of the metal structure is not easy. A visual inspection is possible, but that will just identify the presence of corrosion pits and not their severity. To get a more accurate assessment will require some specialist resources such a sonic, electromagnetic or electrochemical testing.
If you notice the signs of corrosion pit forming it is essential to repair the breach to the protective coating that has caused the issue before it turns the metal object into a block of Swiss Cheese!
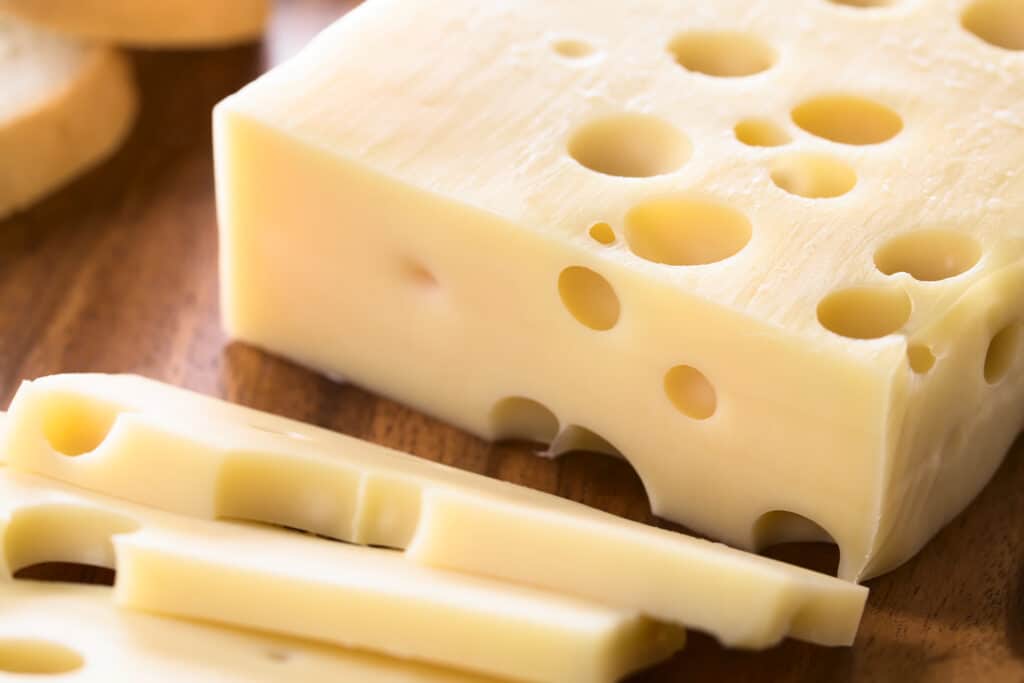